Los adhesivos juegan un papel clave en la construcción de guitarras
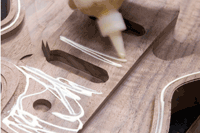
Publicado originalmente en agosto de 2009. Para ver el artículo original, haga clic aquí.
Cuando Leo Kottke toca su guitarra Taylor de 12 cuerdas, el público no piensa en el papel que desempeñan los adhesivos en la música.
De hecho, los adhesivos desempeñan un papel clave en la construcción de los instrumentos, afirma Chris Wellons, vicepresidente de producción de Taylor Guitars. Casi todas las 175 piezas que componen una guitarra de seis cuerdas y las 250 de un instrumento de 12 cuerdas se ensamblan a mano con varios pegamentos diferentes. Wellons dice que alrededor del 95 por ciento de cada guitarra fabricada en la planta de Taylor en El Cajon, California, se ensambla con pegamento de resina alifática amarilla. La fábrica de Taylor Guitars en El Cajón es donde se corta, muele, lija, dobla y termina la madera en bruto para crear los instrumentos musicales.
La compañía fabrica 80 000 guitarras y 15 000 estuches de guitarra al año., y el 95 por ciento de todas las piezas se pegan a mano después de cortarlas. Taylor utiliza diferentes adhesivos para diversas aplicaciones, como Franklin Adhesives Titebond, Multibond 2015, Assembly High Tack, Titebond 50 y Titebond Melamine. Según Wellons, el uso de los productos adhesivos Franklin en Taylor Guitars se remonta a casi 20 años atrás.
«Además de los pegamentos industriales amarillos para carpintería que se encuentran comúnmente en nuestra fábrica, también utilizamos cintas o adhesivos de doble adherencia, pegamento curado por UV, epoxis, cianoacrilatos y una soldadora ultrasónica para adherir las piezas de plástico, como es el caso de los sensores superiores del Expression System», afirma Wellons.
Construcción de guitarras En la fábrica de El Cajón, el proceso de construcción de una guitarra comienza con madera cruda y curada. La caoba es la madera preferida para los cuellos y los cabezales. Una vez fresadas, moldeadas y lijadas ambas piezas hasta obtener su forma final, comienza el proceso de solicitud.
Comenzando en la parte superior de la guitarra, en la unión de la espiga y el mástil, una junta en forma de bufanda une la clavija con el resto del mástil. En esta junta tipo bufanda, se necesita precisión para lograr un ajuste correcto, y se utiliza una ligera aplicación de Titebond 50.
«Una vez que empezamos a usarlo, descubrimos que funcionaba en una variedad de aplicaciones debido a su alta tolerancia a la temperatura», dice Wellons. «Tanto en las articulaciones de los dedos como en las articulaciones de los dedos, descubrimos que el Titebond 50 solo hace que estas áreas tradicionalmente débiles se fortalezcan bajo presión».
Tanto la chapa de clavija como el diapasón, hechos de ébano macizo y denso, se adhieren a la clavija y al cuello con Titebond 50. Se aplica una capa fina y se deja secar el mástil antes de colocarlo en el diapasón.
Titebond 50 también se usa en el interior del cuerpo. para fijar el talonero; en la base del mástil y en el canalón, que se alinea alrededor de la forma del cuerpo para aumentar el espacio de la superficie y adherir la parte superior y la parte posterior a los lados del cuerpo de la guitarra.
En algunos modelos, se utiliza melamina Titebond. Al igual que con los adhesivos mecánicos, la superficie se lija para que los materiales se adhieran, ya que el adhesivo se aplica con una capa de rodillo sobre las piezas a medida que se colocan. La encuadernación en celuloide de marfil y carey y los ribetes de vinilo, el ribete que rodea los cuerpos de las guitarras en varios de los modelos populares de Taylor, se fijan con este método.
Una vez que la parte superior y posterior están unidas a los lados, la guitarra está preparada para su acabado brillante. Si bien la resistencia es el principal beneficio de usar Titebond 50, Taylor Guitars usa una fórmula especial que incluye un aditivo SP fluorescente. Antes de recibir su acabado brillante, cada guitarra se coloca bajo una luz negra para garantizar que no haya pegamento en la parte superior, trasera o laterales del modelo.
«Esta prueba, que utilizamos como uno de los muchos pasos para garantizar la calidad, consiste en raspar y lijar las partes de la guitarra y, luego, sujetarlas bajo la luz negra», dice Wellons. «Cualquier residuo de pegamento se identifica con el aditivo «brillante», que luego se anota y se retira antes de terminar. Franklin suministra el pegamento premezclado con el aditivo que contiene para este paso del proceso de fabricación. En otras partes de la fábrica utilizamos habitualmente el mismo pegamento sin el aditivo».
Tras el brillo y la fijación del mástil al cuerpo, la guitarra llega al área de ensamblaje final de la fábrica, donde se colocará un puente y se ensartará la guitarra. Dado que la tensión entre la clavija y el cuerpo es el factor principal a la hora de doblar el cuello y inclinar el cuerpo, la fuerza de unión del puente y su fijación al cuerpo es vital. En este caso, Taylor utiliza la fórmula Assembly High Tack.
«La tensión en esta articulación, o la tensión que producen las cuerdas, oscila entre aproximadamente 125 y 175 libras», dice Wellons. «La tensión es diferente a la de una guitarra de seis a 12 cuerdas y también puede cambiar según la afinación. El hecho principal es que cuanto mayor es la superficie del pegamento, más fuerte es la unión y, a decir verdad, la unión es siempre más fuerte que la propia madera.
«Durante el proceso de prueba para evaluar los adhesivos, colocamos el mástil de la guitarra sobre una prensa tipo eje, contra una célula de carga, para determinar la resistencia del producto», explica Wellons. «De los muchos productos probados, Titebond 50 tenía la mayor resistencia a la rotura en libras por pulgada cuadrada.
«Realizamos una variedad de pruebas internas e in situ, incluidas pruebas de tensión/carga. Como nuestras guitarras se envían a todo el mundo, es importante medir su rendimiento en diversos climas. De este modo, sometemos los productos a niveles altos y bajos de humedad y a temperaturas variables en una cámara húmica, lo que proporciona un entorno controlado. También utilizaremos pruebas «reales», como enviar guitarras de ida y vuelta a lugares con prototipos hechos con los materiales de prueba, que luego se tocan, se viajan y se golpean un poco para ver cómo se mantienen.
«Multibond 2015 se usa en la cercana ciudad de Tecate, México, donde Taylor fabrica 15 000 estuches de guitarra al año. Aquí, la madera contrachapada pasa por un aplicador con rodillo y se aplica a las fundas de guitarra para lograr un efecto laminado.
Crear una guitarra es un proceso laborioso que puede llevar de ocho a 21 días. El uso de estos adhesivos y los altos estándares de control de calidad de Taylor reducen el riesgo de que surjan problemas de calidad a medida que la guitarra avanza hacia el ensamblaje final. Es posible que el público no se dé cuenta, pero los adhesivos son una parte importante del instrumento terminado.
Corporate Contact
Audrey L. Albright
Technical Marketing Specialist
E: audreyalbright@franklininternational.com
T: 1.800.877.4583
Corporate Contact
Mark Schroeder
Vice President of Marketing
E: markschroeder@franklininternational.com
T: 614.445.1507
Related Products
Alifático
Titebond 50
PVA reticulado
Multibond 2015
More information is available about our complete product offerings. Our experts can recommend specific solutions for your needs.