Pressure Sensitive Glossary
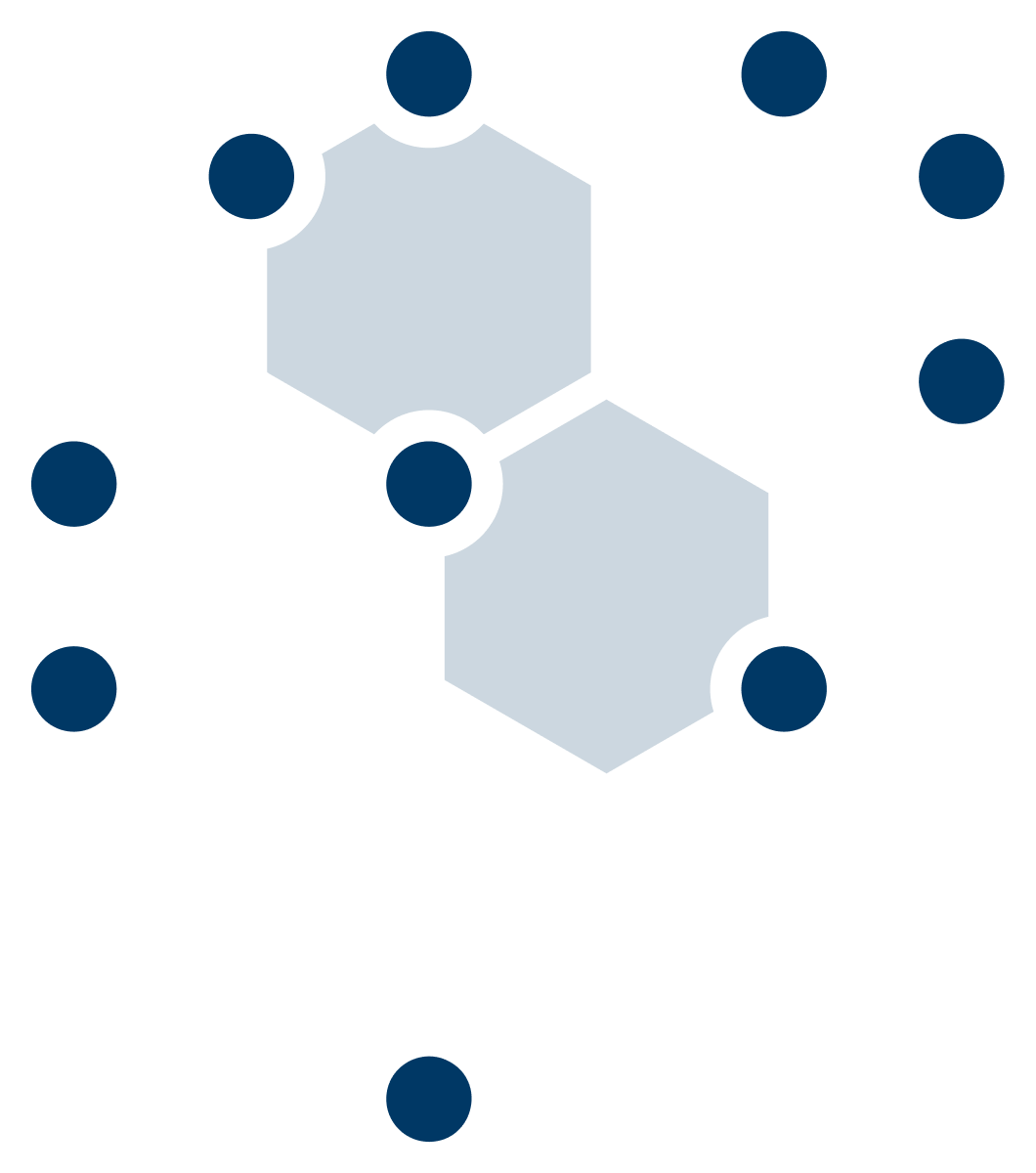
The glossary is designed to provide you with a complete list of unfamiliar terms and their definitions. To move within the page, select the beginning letter of the word you are searching. If you need further assistance, please contact our technical support team.
Adhesive/Cohesive failure
Designations for mode of failure of a peel test. Adhesive failure indicates that the peel strength is less than the cohesive strength; the adhesive comes free of the substrate, remaining on the face stock. Cohesive failure indicates the peel strength is higher than the cohesive strength causing a film split.
Anchorage
A term for how well an adhesive sticks to the face stock of a tape or label. Poor anchorage can cause labels or tapes to transfer.
Back-up roller
A roller that is used to hold the web against another roller. The back-up roller holds the uncoated side.
Coat weight
A measure of the amount of coating on the substrate. This can be expressed in units of thickness (such as mils or microns) or weight per area (such as gm/m2 or lb/ream).
Coater
A device that coats adhesive onto a substrate. Generally consists of a coating head, a drying oven, and unwind / rewind stations for the substrates. May also include stations for other functions such as corona treatment, surface priming, or silicone coating.
Cohesive strength
This is the internal strength of an adhesive. Higher shear products typically have high cohesive strength. May determine mode of failure.
Converting
The process of making finished product from the master rolls off the coater. This may include various combinations of edge trimming, slitting, sheeting, die cutting, scoring, and printing.
Co-polymer
A polymer made from two or more monomers. The monomers used must be able to react together. The Covinax line of products is an example of co-polymers.
Corona treatment
A treatment for films and papers to improve anchorage. The web is treated with a high voltage arc that creates an oxidized layer. The adhesive bonds to the oxides better than to the untreated surface. Often used for self wound films - the adhesive anchors to the treated side, but releases from the untreated side.
Crater
Coating defect where a circular void opens up in the coating on a release liner.
Cross linker
An additive that will cause polymer molecules to inter-connect, effectively increasing the molecular weight of the polymer. Cross linkers generally increase the shear performance, while causing peel and tack to drop.
Cross linking monomer
A monomer that polymerizes in the polymer, then acts as a cross linker when the polymer is cured.
Defoamer
Material used to prevent foam and/or make foam bubbles disperse more rapidly.
Direct coating
Any process where the coating is applied directly to the face stock. A release liner may be applied after drying, or it may be self wound.
Dispersion
Any form of small particles of solid material dispersed in a carrier liquid. Tackifiers and pigments are two examples.
Doctor blade
A straight edged blade that wipes a roller surface clean. On a gravure roll, this will leave only the adhesive that is in the gravure cells. Small doctor blades are used on applicator rolls to clean where the edges will be on the web.
Edge crawl (AKA suck-back)
When the adhesive at the edge of the coating or within a void continues to pull back until the film dries.
Emulsion polymerization
A process for making water based polymers using an emulsion of water, surfactant, and monomer, with a water soluble initiator. The polymerization takes place in the water phase, creating small polymer particles dispersed in water.
Face stock
Any paper, film or other material that the adhesive is coated onto or transferred to. Becomes the label "face".
Ghosting or residue
A film that is left behind when the label or tape is removed, creating a "ghost" image of the label on a smooth surface. This may be caused by materials such as plasticizer, oil, defoamer, or low molecular weight polymer that migrates to the surface of the adhesive layer.
Glass transition temperature (Tg)
The temperature where a polymer transitions from a glassy solid to an elastic material. A polymer needs to be ~30 - 40ΕC above the Tg to be pressure sensitive. Franklin PSA’s are in the range from -80ΕC to -20ΕC.
Gravure coating
Coating using a gravure roller. A gravure roller has a surface covered with a pattern of cells or grooves that meter the adhesive to the web after a doctor blade wipes off the excess.
Homo-polymer
A polymer made from a single monomer. Vinyl acetate homo-polymers like Duracet are an example.
Hot melt (thermoplastic)
An adhesive that is solid at room temperature, but flows when heated. May be a PSA depending on the material.
Laminate
To bring two or more layers together to create a multi-layer construction, such as release liner-adhesive-paper. This is generally done at the rewind station of a coater. Can also refer to the construction made by this process, containing layers of substrates and adhesive(s).
Line speed
The rate at which the web goes through the coater, usually given in ft/min.
Mayer rod - Metering rod
A wire wound rod used for metering the coating onto the substrate. The coating thickness is directly proportional to the wire thickness.Mayer rod coaters use a roller to apply adhesive to the web, then it goes across the mayer rod to meter off the excess. The rod usually rotates to prevent streaks caused by particles caught in the wire grooves.
Metering
The function of the coating device that controls the amount of adhesive that is deposited on the web.
Molecular weight
A measure of how large each polymer molecule is. Higher molecular weight generally improves PSA performance.
Monomer
Any material that will form a polymer when initiated to react. Some common monomers used for PSA manufacture at Franklin are 2-ethylhexyl acrylate (2EHA), n-butyl acrylate (nBA), and vinyl acetate (VAc).
Nip
The point where two rollers come together. At the coating head, this can be where the excess adhesive is metered off of the pickup roll. At the rewind station, this is where the laminate is made.
Oligomer
Either a high molecular weight monomer, or a low molecular weight polymer, oligomers can be included in a polymer to give special properties that the polymer would not have by itself.
Orange peel
Coating defect that resembles the ripples on the surface of an orange. Often caused by defoamer.
Peel strength
A measure of the force to pull a strip of tape off of a substrate. Usually done at a 90 or 180 degree angle. Results are in units of force per unit width. (lb./in. or N/cm)
Ream
A measure of paper area. Usually 3000 ft2 for paper, but can also refer to 3300 ft2 for release liner.
Removable
A low peel adhesive that is designed to come off a surface cleanly, without damaging the label or substrate, and leaving no adhesive residue.
Rheology
A description of how the viscosity is affected by changing shear on the product. Most latex type materials exhibit some degree of shear thinning - as the shear rate increases, the viscosity decreases.
Rills
Coating defects that resemble a corduroy pattern, usually seen in coatings from a mayer rod.
Release liner
A paper or film treated with a silicone coating, used to cover a PSA coating during manufacture and converting of a PSA label Generally peeled off and discarded when the PSA label is used.
Roll coating
A system of coating that uses a combination of 2 or more rollers to meter and apply the coating to the web. Rollers may be polished or rubber coated. Metering is adjusted by changing variables, such as nip gap, roll speed and line speed. If the applicator moves in the web direction, it is called a "direct roll". If it moves opposite the web, it is called a "reverse roll". A common configuration is a 3 roll reverse coater, with a pick-up roll in the adhesive pan, a metering roll, and an applicator roll. There is also a back-up roll to hold the web at the nip.
Self wound
Any coated product that is wound up without using a second layer for release liner. The adhesive coating is wound up onto the back of the substrate. This is how most tapes are coated.
Shear Test
The shear test is the time it takes a sample to fall off a panel, sliding vertically under a constant stress load. Results are in units of time (min. or hrs.)
Slot die
A coater head that uses a narrow slot opening to apply the coating. The coating is metered by adjusting the flow rate of the adhesive.
Smoothing bar
A small diameter roller with a polished face that helps to level the coating immediately after leaving the coating head. It may rotate either with or against the web direction.
Solution polymerization
A process of making a polymer in a solvent solution. The resulting polymer remains in solution.
Solvent based
An adhesive or resin solution that uses an organic solvent such as toluene or hexane to make a solution.
Substrate failure
This is the ultimate mode of failure for a permanent label. This indicates destruction (tearing, stretching, or de-lamination) to either the label or substrate. Also referred to as a destructive bond.
Suspension polymerization
A process for making water based polymers using an emulsion of water, surfactant, and monomer, with a monomer soluble initiator. The polymerization takes place in the monomer, creating solid spheres of polymer.
Tackifier
A dispersion of resin that is used to increase the peel and tack of a PSA. Rosin ester resins are the most common.
Tack test
A measure of the "stickiness" of an adhesive. Loop tack, probe tack, and rolling ball tack are examples of test methods. Results are in units of force. (lb. or N)
Thickener
Material used to increase the viscosity of a liquid. Also important in establishing or modifying the rheology of the liquid.
Transfer coating
Any process where the coating is first applied to the release liner instead of the face stock. The coating is dried on the liner, and then laminated to the face stock. When the liner is removed, the coating will stay on the face stock. This usually produces a smoother coating surface and is necessary when the face stock would be harmed by exposure to high temperatures in the drying oven.
Transfer tape
A construction made with adhesive sandwiched between two release liners, or self wound on a double sided liner (silicone on both sides). The release coatings need to be different (one low, one high) or the adhesive will get "confused", and not transfer cleanly. Transfer tapes are used where the application requires a small patch or strip of adhesive and liner, such as an envelope flap, or where the objects cannot go through a web process, such as 3D objects like decals or plaques.
Transfer
This mode of failure occurs when the peel strength and cohesive strength are higher than the force of anchorage on the face stock. The adhesive transfers from the face stock to the substrate. This is a common problem with low peel adhesives that are transfer coated.
Unwind / Rewind
Stations at either end of the coater that hold the rolls of product used or made on the coater. The unwind stations hold the uncoated products and feed them to the coater. The rewind station winds up the material coming from the laminator.
Wetting agent
Material (usually a surfactant) used to lower surface tension and improve the coating surface.
Water based
An adhesive or dispersion that uses water as the carrier.
Web
The material that is fed through a coater in a continuous sheet.
Corporate Contact
Audrey L. Albright
Technical Marketing Specialist
E: audreyalbright@franklininternational.com
T: 1.800.877.4583
Corporate Contact
Mark Schroeder
Vice President of Marketing
E: markschroeder@franklininternational.com
T: 614.445.1507
Related Products
More information is available about our complete product offerings. Our experts can recommend specific solutions for your needs.